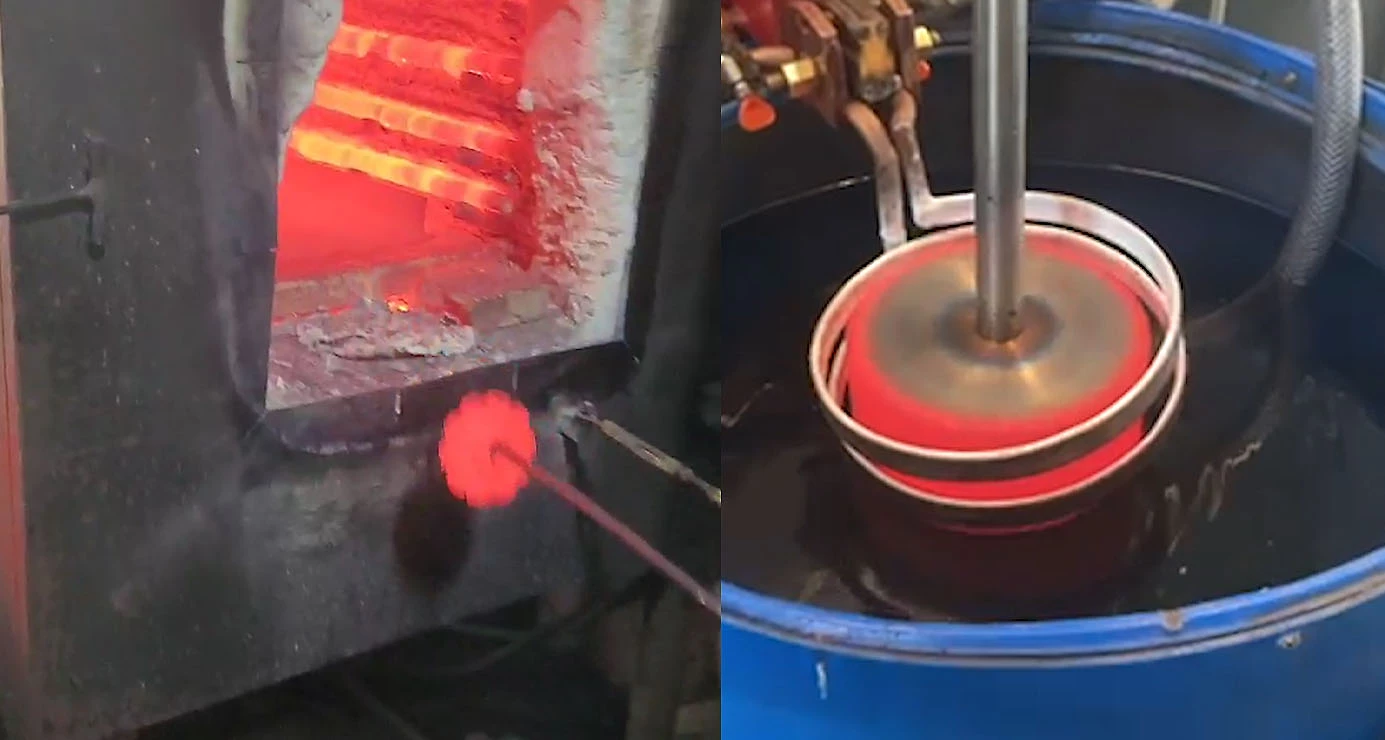
Custom Sprocket Manufacturing by Bas-Agro Group LLC
Bas-Agro Group LLC offers custom sprocket manufacturing services. We provide high-quality production of sprockets for various industries, ensuring precision, durability, and longevity of each product. Watch the video of thermal processing of a sprocket on our YouTube channel.
Our Advantages:
- Individual Approach: We take into account all the requirements and wishes of the client, creating sprockets that perfectly meet your needs.
- High-Quality Materials: We use only verified materials, ensuring the reliability and durability of the products.
- Modern Technologies: Our equipment and technologies allow us to produce sprockets with high precision and in short terms.
- Thermal Processing: We provide a hardening process to increase the hardness and wear resistance of the sprockets.
- Quality Control: Each detail undergoes strict quality control at all stages of production.
Contact us:
- by phone: +380675101562
- at the address: Khomenko Lane 8/1, Cherkasy
- browse the catalog of finished products - spare parts for agricultural machinery on our website bas.ua
Choose a reliable partner in sprocket manufacturing - Bas-Agro Group LLC!
Technological Stages of Sprocket Manufacturing
Design and Drawing Development
- Development of technical specifications and creation of drawings according to the customer's requirements.
- Use of CAD programs for sprocket modeling.
- Verification and approval of the project.
Material Selection
- Selection of the appropriate material (usually steel, cast iron, or other special alloys) considering the requirements for strength and wear resistance.
- Purchase of material and quality inspection.
Preparation of Blanks
- Cutting blanks from the selected material to the required sizes.
- Preliminary processing of blanks (turning, milling) to achieve the desired shape and dimensions.
Mechanical Processing
- Turning: forming the main geometric dimensions of the part on a lathe.
- Milling: processing of the surfaces and chamfers of the blank on a milling machine.
Tooth Formation
- Milling: cutting teeth on special gear hobbing machines using disc cutters.
- Broaching: additional processing for forming precise tooth profiles.
Thermal Processing
- Hardening: heating the part to a high temperature followed by rapid cooling to increase hardness and wear resistance.
- Tempering: heating the part to a certain temperature followed by slow cooling to relieve internal stresses and improve mechanical properties.
Finishing
- Grinding: grinding the teeth to achieve precise geometry and high surface quality.
- Polishing: polishing the surface of the sprocket to improve appearance and reduce friction.
Quality Control
- Visual inspection: checking the appearance and absence of defects.
- Parameter measurement: precise measurement of the dimensions and geometric parameters of the part using special equipment.
- Compliance check: control of the manufactured part's compliance with the technical specifications and quality standards.
Final Operations
- Washing and degreasing: cleaning the part from residues of technological fluids and other contaminants.
- Anti-corrosion treatment: applying a protective coating to prevent corrosion.
- Packaging: packaging the finished products for transportation and storage.
Sprocket manufacturing is a complex technological process that includes several stages. Each of these stages is critical to ensuring the high quality and reliability of the final product. High precision at all stages of production ensures the durability and efficiency of the sprockets in operation.
Add a comment
Comments
There are no comments yet. Be the first to comment.
You must be logged in to post a comment
Login