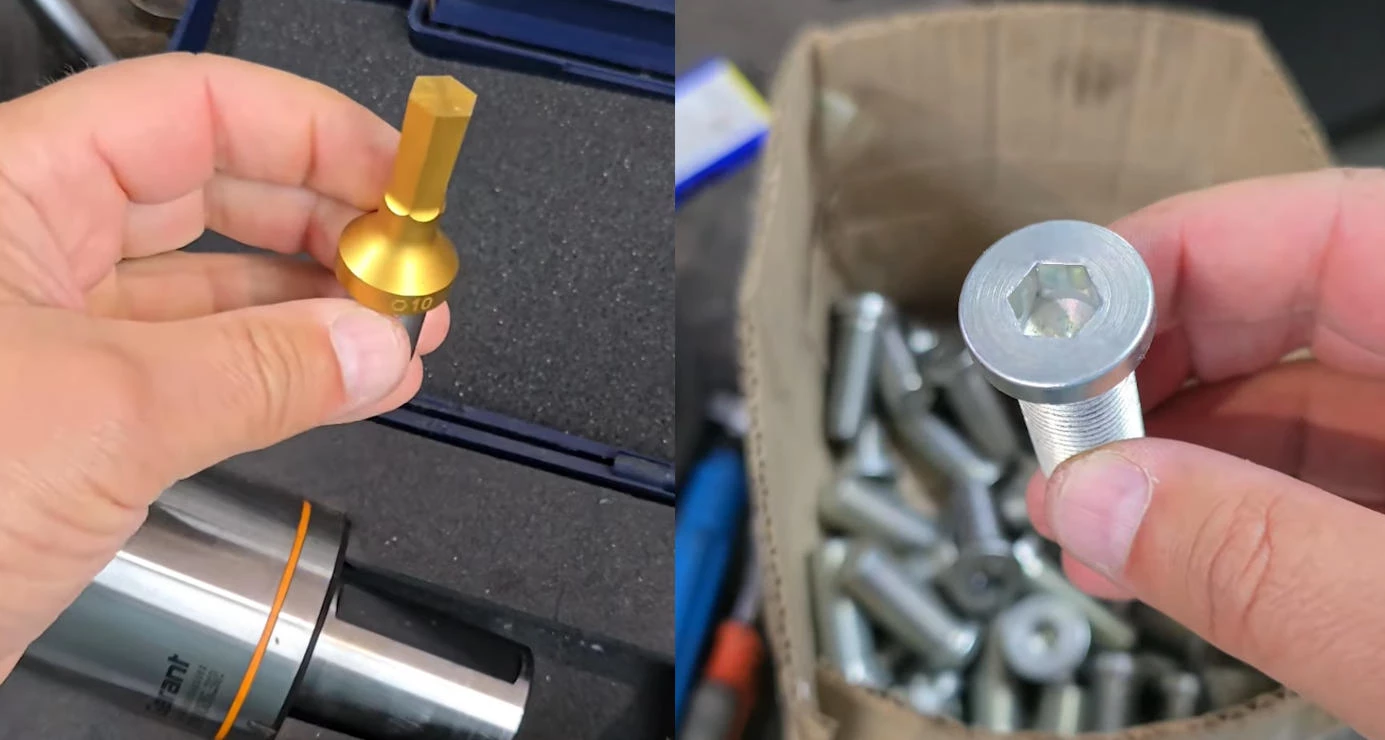
Rotary Broaching on CNC Lathes
1. What Is Rotary Broaching and How Does It Differ?
Rotary—or “wobble”—broaching is a way to produce polygonal holes or external flats without a separate broaching press: the tool is mounted in a special holder at an angle of about 1° to the work‑piece axis. As the spindle turns, a single cutting edge enters the material in sequence and, like a pencil, “draws” the profile of a hex, square, Torx or spline in just a few seconds—practically within one spindle revolution.
Because only one point cuts at a time, axial force is roughly 80 % lower than in punch or pull broaching, and machine/tool wear drops dramatically.
See the video of an internal hexagon being made on a CNC lathe via rotary broaching.
2. How It Works from a Process Engineer’s Viewpoint
- Wobble angle. The built‑in 1° tilt creates a rolling action of the cutting edge.
- RPM synchronisation. The broach sits in a floating spindle and turns 1:1 with the part—no live tooling required.
- Feed. Ideal feed f ≈ d × sin θ (with θ = 1° this is ≈ 1.7 % of diameter per rev). Lower feed reduces load; higher feed worsens surface finish.
- Depth. Safe working depth is 1.5 × minimum profile diameter; in soft alloys up to 2 × AF (across‑flats) is achievable.
Pro tip: Drill the pilot hole 3% larger than the hex key size (10 % for squares). It chips swarf better and extends broach life.
3. Advantages over Classical Push/Pull Broaching
- Speed. Cycle time is 5–20 s; the part leaves the lathe finished.
- Accuracy. Premium broaches are ground to ± 0.0005″ (± 0.013 mm), so the feature is in‑tolerance immediately.
- Lower CAPEX. No need for a broaching machine or hydraulic press—your existing CNC lathe or Swiss‑type is enough.
- Blind‑hole capability. Unlike pull broaching, a rotary broach doesn’t need through‑holes, perfect for many agri‑mechanical hubs.
- Reduced machine wear. Load is absorbed by the broach holder, not by the spindle bearings.
4. Technical Limits & Typical Cutting Data
Parameter | Value |
---|---|
Shape range | Internal/external Hex, Square, Torx, splines & custom polygons Ø 3–50 mm |
Materials | Carbon & alloy steels, 304/316 stainless, 6xxx aluminium, brass, Ti Grade 5 (with TiN, TiAlN coatings) |
Spindle speed | 1000–2500 rpm for steels; up to 3500 rpm for Al |
Coolant | Flood ≥ 20 bar or MQL for blind holes |
Service life | Broaches can be reground 3–5 times without losing geometry |
5. Why Does Agribusiness Care?
Seed‑drill gearboxes (Kverneland, Monosem) and sunflower headers (Zaffrani) often need internal hex couplings, spline sleeves or key‑flats. Rotary broaching lets you:
- Shorten the route: lathe → press → grind shrinks to a single set‑up.
- Boost serviceability: precise geometry ensures field‑ready interchangeability of spare parts.
- Cut cost: shorter cycles and no “bottleneck” broaching press.
6. What Bas‑Agro Offers
Rotary broaching of internal profiles Ø 3–25 mm.
Full CNC cycle: turning, milling, threading, heat‑treating, grinding.
100 % QC (3‑D CMM, optical microscope, hardness tester).
Small‑ and mid‑volume parts for ag‑machinery, hydraulics and precision mechanics.
Send your drawings to [email protected] or call +38 (067) 470‑35‑44—we’ll help you create blind internal polygons.
Rotary broaching marries the flexibility of a CNC lathe with the speed and economy of dedicated broaching. For agricultural OEMs it means polygonal parts that are more accurate, faster and cheaper to make. Bas‑Agro already runs the technology and is ready to scale it for you—from prototypes to mass production.
Check our catalogue of ag‑machinery spare parts.
Rotary broaching—shorter cycles, bigger harvests for your business!
Add a comment
Comments
There are no comments yet. Be the first to comment.
You must be logged in to post a comment
Login