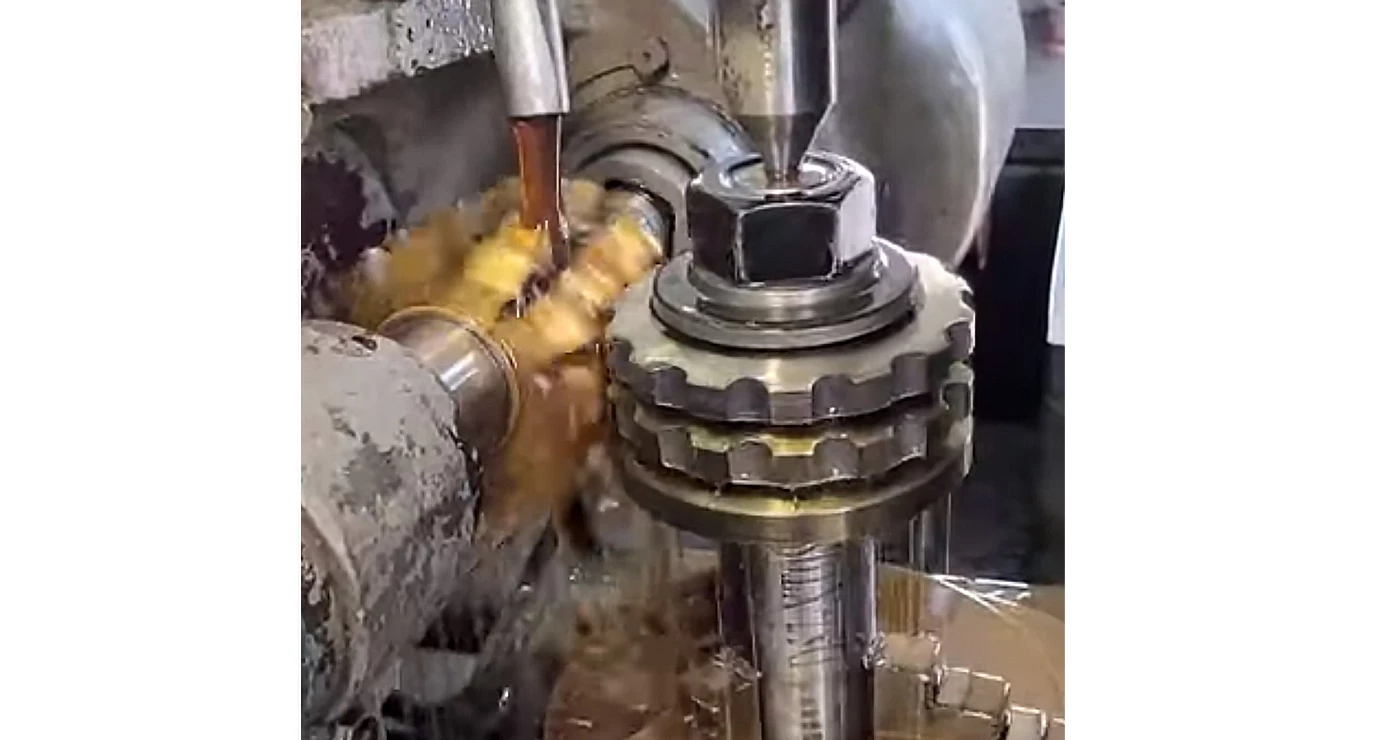
Gear Hobbing: Metalworking for Sprocket, Gear, and Gear Wheel Manufacturing
Gear hobbing is one of the primary metalworking methods used for manufacturing sprockets, gears, and gear wheels. This process ensures high precision and quality, which are critically important for the reliability and durability of mechanical systems.
Gear Hobbing Services from Bas-Agro Group LLC in Cherkasy
Bas-Agro Group LLC offers top-quality gear hobbing services. The company uses advanced equipment and highly skilled specialists to ensure the accuracy and reliability of each manufactured product. On the website bas.ua, you can learn more about the range of other metalworking services provided and order the necessary work for your business.
To order gear hobbing services, contact us:
- By phone: +380675101562
- At the address: Cherkasy, Khomenko Lane 8/1
- On our website https://bas.ua with a catalog of spare parts for agricultural machinery.
Let's take a closer look at the gear hobbing technology, its advantages and features, as well as examples of its application in the industry.
Gear Hobbing Technology
Gear hobbing is the process of machining metal blanks using a special tool called a hob to form the tooth profile of a gear or sprocket. The main stages of this process are:
- Blank Preparation: Selection of material and preliminary processing, which includes turning to give the blank the necessary dimensions and shape.
- Hob Selection: The hob is selected depending on the type and size of the teeth to be formed. Various types of hobs exist, such as conical, cylindrical, and modular.
- Hobbing Process: The blank is fixed in the machine, and the hob begins to rotate at high speed, gradually cutting the material and forming the teeth.
- Quality Control: After hobbing is completed, thorough quality control is conducted to ensure accuracy and compliance with parameters.
- Heat Treatment.
Advantages of Gear Hobbing
Gear hobbing has several advantages over other methods of gear manufacturing:
- High Precision: The process allows achieving very high machining precision, which is crucial for torque transmission and wear reduction.
- Surface Smoothness: Special hobs can achieve a high level of tooth surface smoothness, enhancing efficiency and reducing operational noise.
- Processing Speed: Modern hobbing machines significantly reduce the processing time of blanks, increasing production efficiency.
- Versatility: Gear hobbing is suitable for machining various types of metals, including steel, cast iron, aluminum, and other alloys.
Application of Gear Hobbing in Agricultural Machinery
Sprockets and gears are integral components of many agricultural machinery units. They are used in tractors, combines, seeders, harvesters, and other mechanisms. The main units where sprockets and gears are applied include:
- Transmission Systems: They provide power transfer from the engine to the machine's working parts. Sprockets and gears help efficiently transmit torque, which is essential for the movement and operation of the machinery.
- Drive Systems of Working Parts: These include the drives of cutting mechanisms, transport systems, and other working parts of agricultural machines. Sprockets and gears ensure synchronization of different parts of the machine.
- Attachment Equipment: Includes devices such as seeders, mowers, and harrows, where sprockets are used to transfer motion from the main machine to the working parts.
Causes of Sprocket and Gear Wear
Sprockets and gears in agricultural machinery are subjected to significant loads and operate in conditions of high dust and moisture. The main causes of their wear include:
- Mechanical Wear: Constant friction between the teeth leads to their wear, especially when working under heavy loads.
- Corrosion: Moisture and chemicals used in agriculture can cause corrosion of metal surfaces, reducing the lifespan of parts.
- Impact Loads: Frequent impacts and vibrations during machine operation lead to tooth damage, which can cause breakage.
- Improper Maintenance: Insufficient lubrication and irregular maintenance can significantly accelerate the wear process.
Gear hobbing is an indispensable metalworking method for manufacturing high-quality sprockets, gears, and gear wheels. Due to its high precision, processing speed, and versatility, this method is widely used in various industries, especially in agricultural machinery. If you are looking for a reliable partner for such work, Bas-Agro Group LLC will be your best choice, offering professional gear hobbing services.
Useful Information: Other types of metalworking performed by our company.
Add a comment
Comments
There are no comments yet. Be the first to comment.
You must be logged in to post a comment
Login