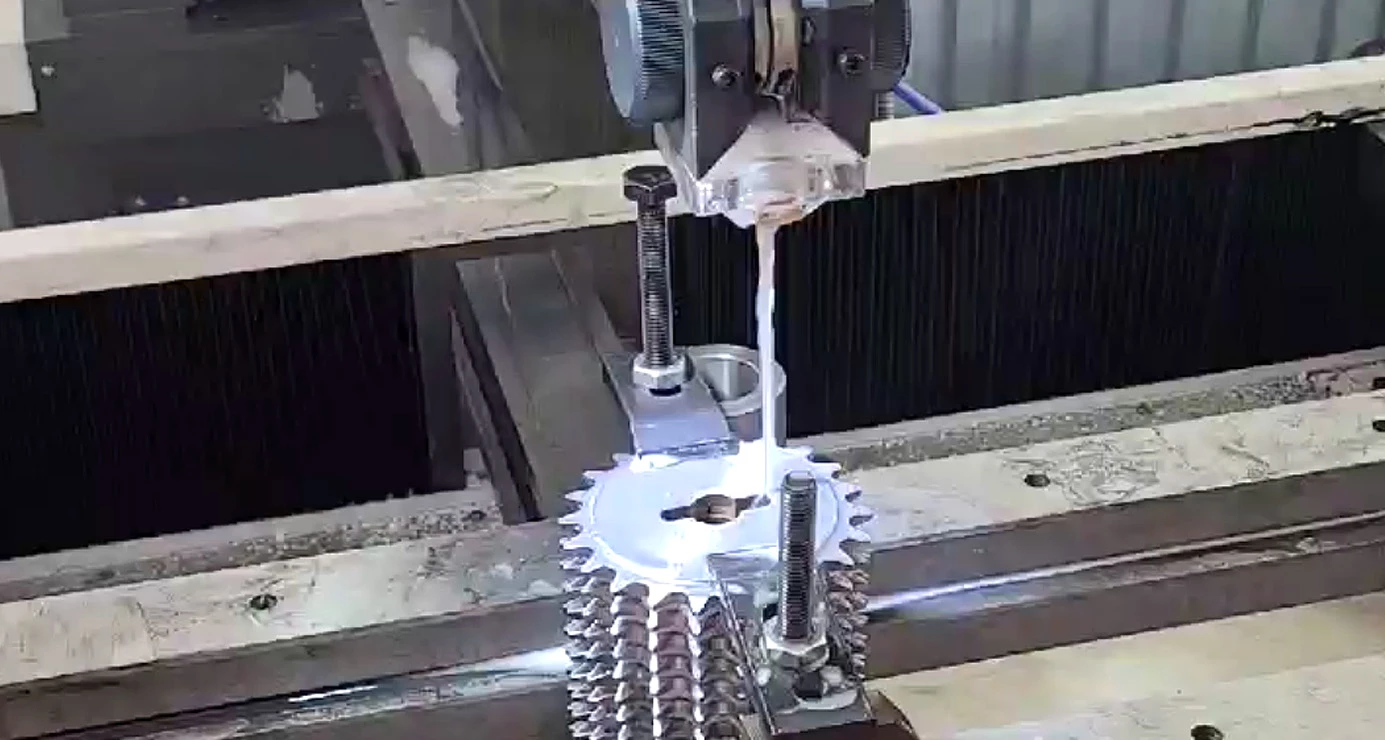
Electrical Discharge Machining (EDM) - a Service Provided by Bas-Agro Group LLC
Modern metalworking demands high precision and the ability to work with a wide variety of materials. One of the most effective methods to achieve these goals is electrical discharge machining (EDM). This method has numerous advantages and is widely used in various industries. Bas-Agro Group LLC offers its clients solutions in this field, ensuring high quality and efficiency in manufacturing processes.
Services from Bas-Agro Group LLC
Bas-Agro Group LLC provides electrical discharge machining services. The company uses the most advanced equipment and technologies to ensure the highest quality of products.
Detailed information:
- Phone number: +380675101562
- Address: Khomenka Lane 8/1, Cherkasy
- On our website with a catalog of spare parts for agricultural machinery: https://bas.ua
- Video of the electrical discharge machining process at our production facility.
Bas-Agro Group LLC is always ready to become your reliable partner in the world of high-precision metalworking, providing the best results for your business. Thanks to the use of innovative technologies and highly qualified personnel, the company guarantees high-quality execution of even the most complex orders.
What is Electrical Discharge Machining?
Electrical discharge machining (EDM) is a method of metalworking that uses electrical discharges to remove material from a workpiece. This process takes place in a special dielectric medium, which allows for high precision and the ability to machine extremely hard materials, such as carbides and hardened steel.
How Does an Electrical Discharge Machine Work?
The main components of an electrical discharge machine include the electrode, dielectric fluid, control system, and power supply. The process follows this sequence:
- Electrode and workpiece preparation: The electrode, which is shaped like the required part, is installed in the machine.
- Immersion in dielectric fluid: The electrode and workpiece are immersed in the dielectric fluid, which cools and removes erosion products.
- Electrical impulses: Electrical discharges are generated between the electrode and the workpiece, which evaporate and melt the material.
- Process control: The control system continuously adjusts the machining parameters to ensure the required precision and quality.
Advantages of Electrical Discharge Machining
- High precision: Allows for achieving micron-level accuracy, which is critically important for high-tech industries.
- Hard material machining: Capable of machining extremely hard materials that are difficult or impossible to machine by other methods.
- Complex geometry: Ability to produce parts with complex geometries.
- No mechanical stress: The absence of mechanical contact during machining eliminates deformation and mechanical damage.
Popular Models of Electrical Discharge Machines
Globally, the most popular models of electrical discharge machines come from leading manufacturers such as Mitsubishi, Sodick, and Makino. Each of these machines has its own features and advantages:
- Mitsubishi MV2400-S: Known for its high precision and reliability, ensuring stable machining quality over a long period.
- Sodick AG60L: This model offers high machining speed and the ability to work with the hardest materials.
- Makino U6 H.E.A.T.: Specifically designed for high-speed machining with minimal electrode wear.
Cost and Speed of Machining Comparison
The cost of work and machining speed depend on many factors, including the complexity of the part, the material being machined, and the chosen machine model. Generally, the cost of electrical discharge machining is higher than traditional methods due to the high operating costs of electrodes and dielectric fluid. However, the high precision and ability to machine extremely hard materials justify these costs.
Add a comment
Comments
There are no comments yet. Be the first to comment.
You must be logged in to post a comment
Login