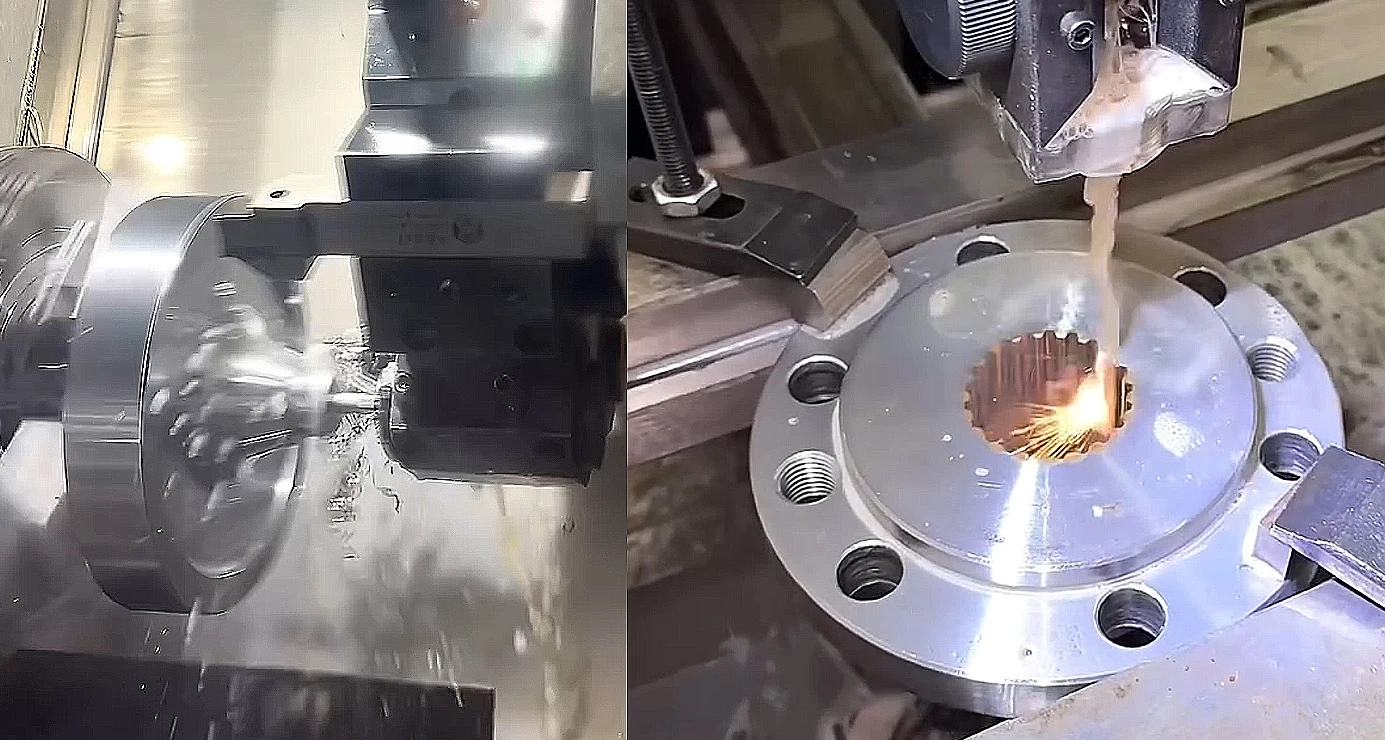
Comprehensive Metalworking: An Effective Solution for Modern Manufacturing
Comprehensive metalworking is an integral part of the modern manufacturing process, ensuring high quality and precision in the production of various parts. This approach includes numerous types of metal processing, such as turning, milling, gear hobbing, laser cutting of metal, as well as finishing stages like powder coating. Ordering all these services in one place significantly simplifies the production process, reduces costs, and increases efficiency.
SERVICES OF COMPREHENSIVE METALWORKING at bas.ua:
- CNC turning,
- milling,
- gear hobbing,
- laser cutting (up to 16mm),
- bending,
- powder coating,
- electrical discharge machining.
You can order these services by calling: +38 067 472 76 10.
A video showcasing examples of comprehensive metalworking at the production facilities of LLC Bas-Agro Group.
Advantages of Comprehensive Metalworking
Saving Time and Resources
The ability to order all necessary types of metalworking in one place eliminates the costs of transporting parts between different companies. This not only saves time but also reduces logistics expenses. Moreover, centralizing production processes allows for quicker responses to changes and the correction of potential processing issues.
Improving Product Quality
Performing all processing stages at one company ensures strict quality control at each step. This reduces the likelihood of defects and allows for high precision in part manufacturing. Each stage, from initial processing to final painting, is supervised by one team of specialists, enhancing the consistency and quality of the final product.
Convenience for the Customer
Ordering all necessary types of metalworking in one place significantly simplifies project management. Customers can focus on their core business tasks without being distracted by coordinating the work of different suppliers. This allows for more effective production planning and ensures timely order fulfillment.
Example of Comprehensive Metalworking
Consider an example where the production of various parts requires turning, milling, gear hobbing, laser cutting of metal, and powder coating as the final stage.
Turning
Turning allows for the production of parts with high precision and surface quality. Using CNC machines automates the process, minimizing the risk of errors and increasing production efficiency.
Milling
Milling is used to process flat and shaped surfaces, produce slots, holes, and other elements. Using CNC milling machines allows for the production of complex parts with high precision.
Gear Hobbing
Gear hobbing is used to manufacture gears and other transmission elements. This type of processing ensures high precision and quality in the production of gear elements, which is crucial for the reliability and durability of mechanisms. We manufacture gears, gear wheels, and sprockets in Cherkasy.
Laser Cutting of Metal
Laser cutting of metal allows for the quick and precise cutting of parts with complex contours. This method is characterized by high accuracy and clean cuts, reducing the need for additional edge processing.
Internal Spline Cutting on a CNC Electrical Discharge Machine
Electrical discharge machining is used for the production of complex internal splines that cannot be made using conventional mechanical methods. This method provides high precision and surface quality even for complex profiles. Using CNC machines automates the process and ensures high repeatability of results.
Powder Coating
Powder coating is the final stage in part processing, providing protection against corrosion and giving an aesthetic appearance. This coating method is highly resistant to mechanical impacts and environmental influences, ensuring the durability of the coating.
Comprehensive metalworking is an effective solution for modern manufacturing, allowing for cost reduction, improved product quality, and simplified project management. The ability to perform various types of metal processing in one place, such as turning, milling, gear hobbing, laser cutting of metal, and powder coating, significantly increases efficiency and convenience for customers. Modern technologies and equipment enable high results and ensure competitiveness in the market.
Add a comment
Comments
There are no comments yet. Be the first to comment.
You must be logged in to post a comment
Login